The essence of economic fabric? By definition, the system of producing and managing material wealth from design to end product. From crop to clothing via scutching, weaving and knitting: Normandy has helped France make a name for itself as the home for every component of its world-renowned high quality flax. Normandy’s La French Filature in Eure has been involved in relocalising a bygone craft, flax wet spinning, to bring the value chain full circle in 2022.
Eco-friendly fibre
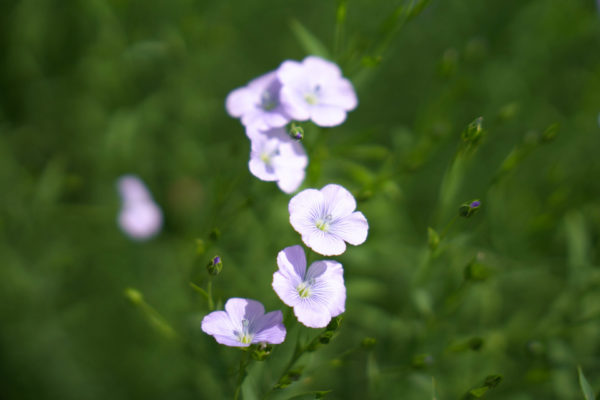
Flax is seen as eco-friendly fabric and has one huge advantage: it grows with minimal inputs and likes a mild climate switching between bright sunshine and heavy showers. It doesn’t guzzle water so it doesn’t need irrigation, unlike its famous cousin cotton. The natural plant fibre has always grown in Normandy and has been popular in the textile industry for years because of its heat control and durability.
Nothing goes to waste in flax: the entire plant is used in a range of sectors. The long fibres are used in textile, the short fibres in paper and composites, the shives in combustibles for heating or particle board. Aside from clothing, it goes into tents, car doors, plane seats, tennis rackets, concrete, insulation boards and more.
Normandy’s fields burst with the little blue blooms in mid-June and account for up to 70% of production in France, estimated at 130,000 hectares or 61% of global production.
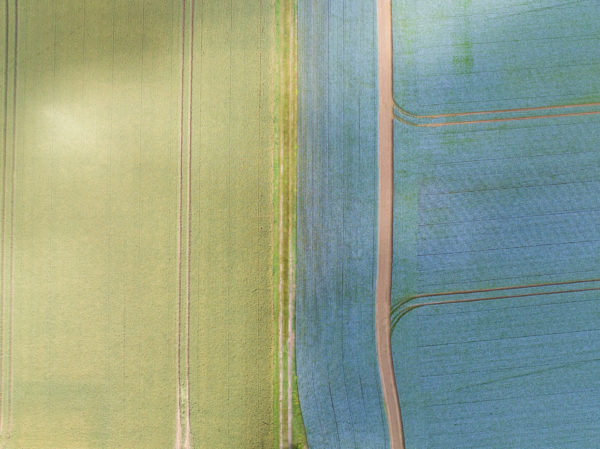
From crop to clothing
The first thing to understand is that there are several stages involved in turning the seed into flax then linen. That’s what makes the sector and its businesses so important. Once it reaches maturity, the entire length of the plant is placed in the soil before retting begins. Retting is a natural process using rainwater to decompose the non-fibrous parts of the stalk without the use of chemicals. The flax is then harvested and undergoes scutching to extract the fibre without the use of chemicals. Then it’s combing time to align the fibre in parallel to produce smooth and shiny yarn. The yarn is then spun ready for use to produce textiles.
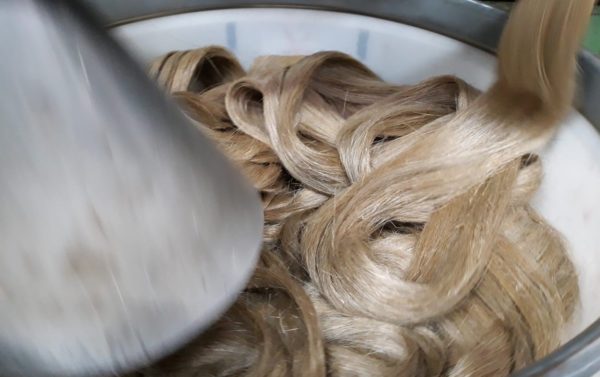
This process often involves several areas of expertise. Just take spinning, that died out in the late 90s in France. Why? Asian imports and the boom in synthetic materials threw the labour-intensive business model off course. “Basically, farmers in Normandy produce the raw material and process it in the region. The long fibres are then exported to India or China to make yarn, fabric and clothes that are sold in France with a label saying Made in China or Made in Bangladesh,” says Karim Behlouli, director of the fibre department at the NatUp agribusiness cooperative.
The nonsensical and carbon-heavy system was called into question when a small proportion of production and flax wet spinning were relocated in 2022.
Relocation: a 100% French industry
The NatUp group is among the brains behind the relocation in France. “Following consumer demand, we set up the first flax and hemp wet spinning mill in 21st century France. It was the missing link in the French industry,” says Karim Behlouli, director of NatUp Fibres that brings together EcoTechnilin in Eure, Seine-Maritime and Poland, Lemaitre Demeestere in Northern France and La French Filature.
La French Filature is located on the EcoTechnilin flax combing and preparation site in Saint-Martin-du-Tilleul and has been producing the finest “wet spun” yarn since 2022. It’s ideal for weaving and knitting textiles to make clothes and household linen. The local, high standard and traceable product has won over several French workshops including MIJUIN, an award winner at the last Normandy Economy Awards. “The service provided by La French Filature is exactly what weavers, manufacturers and brands are looking for to make 100% linen products made in France,” says the director.
It’s now time for the group to get big brands on board with French flax: several key figures, including La French Filature and NatUp Fibres, joined forces to launch a collaborative platform for industry players on June 22nd 2023. It’s called Bleu Blanc Lin and it has the support of the Textile Industry Union. Just like its hemp cousin Bleu Blanc Chanvre, the aim is to revive the French flax industry with an action plan over the next three years.
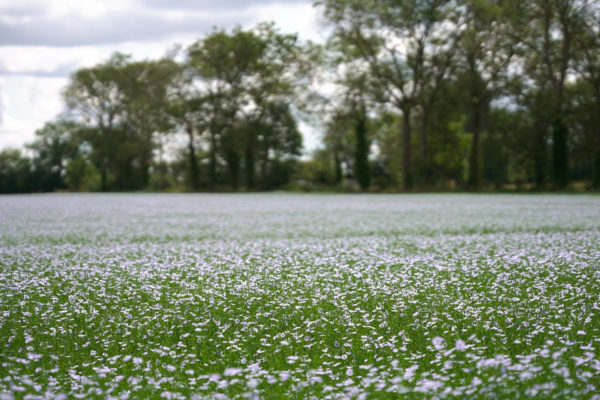
Good to know
- La French Filature bought 14 new spinning machines with an investment of 4.4 million euros, co-funded by NatUp, the Normandy Region and French government.
- NatUp is an agribusiness group uniting 7000 farmers and 5000 members in Normandy, Picardy, Île-de-France, Eure and Loire. The cooperative helps farmers towards sustainable and quality agriculture and helps sell their grains, cattle, sheep and vegetables. The group has 4 departments: grains, vegetables, fibres and rural distribution. NatUp works with 1800 people and makes 1.6 billion euros in turnover.
- The Saint-Martin-du-Tilleul facility can make up to 250 tons of yarn per year, the equivalent of 1.25 million shirts, 750,000 yoga pants and 300,000 bed sheets.
- To ensure the standard of the yarn is in line with customer requirements, La French Filature has a quality control laboratory to check the incoming fibres meet specifications. It also ensures features such as yield strength, finesse, colour and consistency comply with the order criteria.
- Normandy leads the way in flax production. It isn’t just the textile industry that has an interest in the plant and its processing: aerospace, automotive and water sports also want a slice of the action.
Just take Depestele, a Seine-Maritime business specialising in scutching (the first process the plant undergoes) mainly for textile company clients. It was selected by the French Government’s 2030 “Prosperity” project with a budget of 1.5 billion euros and in partnership with ENSICAEN and Université de Caen. The collaborative project supported by the French state aims to remove any obstacles impeding the roll-out of flax materials, to design and industrialise production to find ways to reuse and recycle the material made entirely from renewable resources.
Thematics