In the workplace, the different kinds of harm caused by regular exposure to noise are recognised today, such as tension, tiredness, difficulty in concentrating, irritation or hearing loss. In order to combat these problems, Laurent Capellari founded Cotral Lab 26 years ago, at Condé-sur-Noireau, in the Norman county of Calvados. His aim? To provide custom-moulded hearing protection devices to workers exposed to sound pollution. Today, Cotral Lab is a world leader: from SMEs through to large corporations, this business had over 2 million users who work in difficult environments. It can count on its 250 staff, over 4 continents, and a turnover of €50m, 25% of which is from export.
Health in the workplace – an essential issue
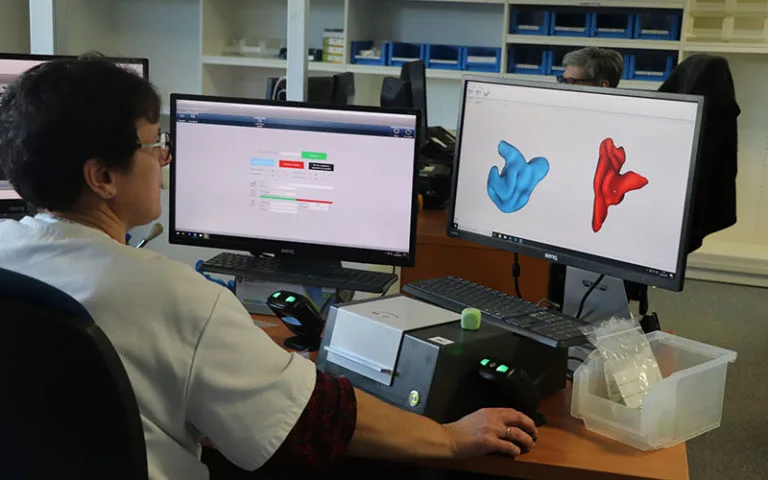
‘‘Acutely aware of the problem, Laurent Capellari created his business all by himself, personally getting involved in every stage, from taking ear-canal moulds to marketing,’’ explains Arnaud Leboucher-Verneau, now head of marketing at Cotral Lab. ‘‘It’s been a significant issue for businesses. With Corporate Social Responsibility on the agenda, he understood that these protection devices provided a concrete response to the problem, benefiting both employer and employee.’’ Finding key players, including Gwenolé Newer, director of technology, performance and transformation, Laurent Capellari rapidly developed his business, both on the technical and organisational sides.
Regulations oblige companies to equip their workers with hearing protection devices from 85 decibels upwards, and to propose them from 80 db.
Having grown across France over 15 years, Cotral opened up to international markets a dozen years ago, notably in Germany, Belgium, Switzerland, Australia and the Nordic countries, before taking on Italy and Spain. ‘‘If hearing loss is diagnosed in an employee at work, the company is held responsible. So it’s in a company’s best interests to protect its workers properly… Our mission is none other than to ensure that employees no longer become deaf because of noise in the workplace, our value proposition really being capable of making a difference all over the place…,’’ makes clear Ricardo Allamelou, Director of International Development. Today, the company is N°1 in the world in the particular segment that is custom-made hearing protection devices, and is proud to have equipped almost two million employees across the world, in over 30,000 businesses of all kinds. ‘‘Most major industrial groups and thousands of SMEs have adopted this solution, but also more surprising groups, like the Miami Fire Brigade.’’
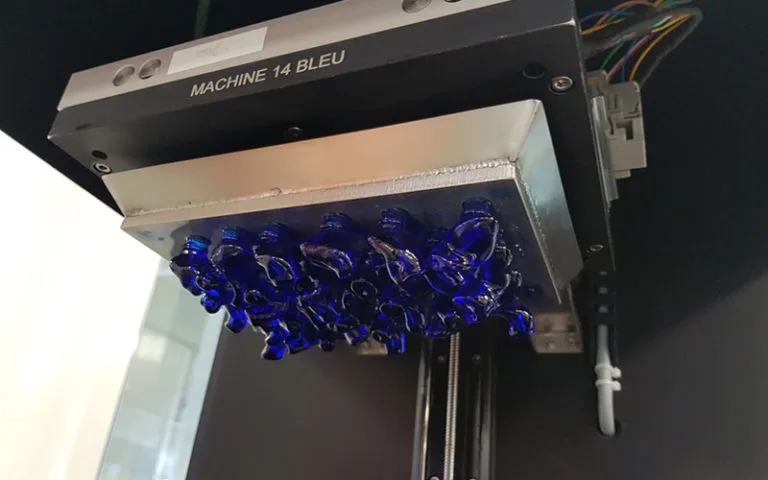
Custom-moulded using innovative processes
Down the years, several models of hearing protection device have been developed in-house by Cotral Lab’s engineers. The challenge? To make these protection devices as comfortable as they are efficient, so that they can be worn with ease through all the periods when a worker is exposed to noise. ‘‘We often make the comparison with rain. If you only open your umbrella a minute after it’s begun to rain, you’ll get wet. It’s the same with noise. There’s an impact even after a short period,’’ Arnaud Leboucher-Verneau emphasises… with the distinction that hearing impairments are invisible and irreversible… To overcome this difficulty, Cotral systematically sensitises employees to the risks of noise. ‘‘A technician specialising in prevention goes into each company, takes the moulds and trains the workers on the importance of protecting themselves from noise pollution.’’ Now, Cotral hearing protection devices are suitable both in loud industrial environments, open spaces and offices.
Working in environments subject to 92db or 87db of noise requires two different kinds of hearing protection devices. It’s the same if you need to communicate regularly with colleagues or not.
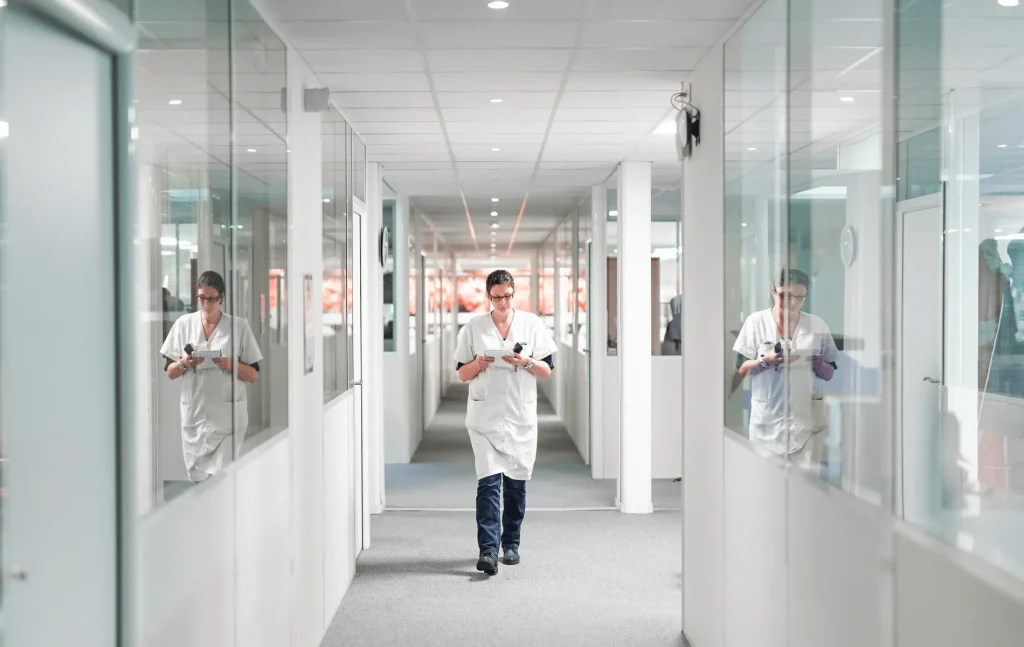
The aims? Comfort and adaptability. ‘‘The different devices are adapted to different work environments, as well as to the hearing and shape of the individual employee.’’ Hence personalised hearing protection devices with handles to make them easy to pick up, or transparent and flat ones, more discreet in an office… To increase the efficiency of the products, the manufacturing process is regularly improved upon. Notably, moulded earplugs made by hand have been replaced by resin hearing protection devices made by 3D additive manufacturing, to ensure maximum airtightness. The complete digitalisation of the process has been developed in-house, allowing Cotral employees to gain in skills and versatility with each manufacturing shift. But Cotral’s expertise comes into play most notably thanks to the acoustic filter linked to the tip of its devices. Like mini-tympanums, these filters, now developed in-house, can eliminate or lessen noise on specific frequencies. ‘‘That’s where the technology is, in the filter; it’s the key element in our hearing protection devices, and the right one can be chosen according to the working conditions of each user,’’ Ricardo Allamelou underlines.
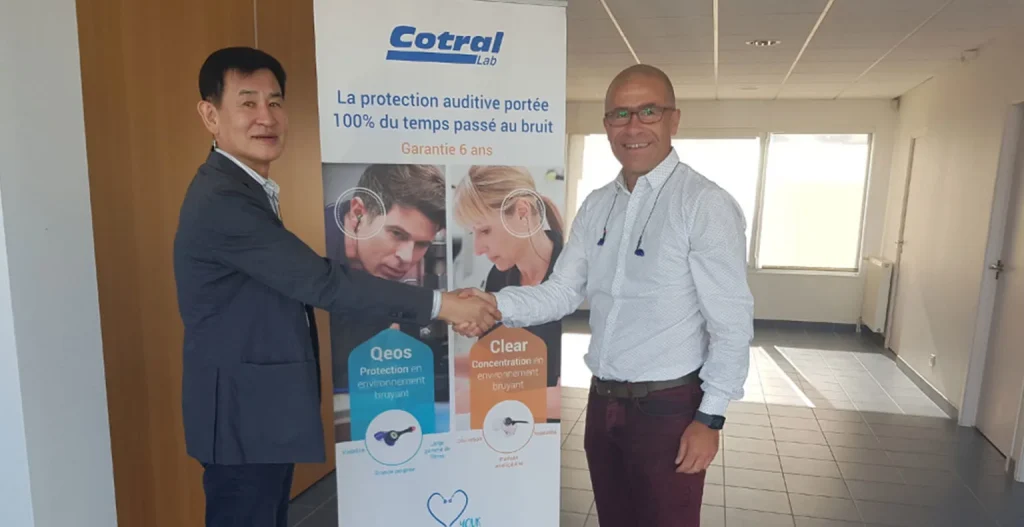
Two major axes: innovation and internationalisation
From improving existing solutions – e.g. release of the cord from 17 newtons upwards, or flatter interchangeable filters – to 4.0 industrial protections, the company has placed innovation as the central pillar for its development. Cotral Labs designs, makes, and distributes two new made-to-measure ranges: prescription security glasses since 2020 and, since 2021, adaptive communications systems for critical and security environments. Cotrel Labs were chosen a few years ago to develop BANG (Bouchon Auriculaire de Nouvelle Génération, or new generation earplugs) for the French DGA (Direction générale de l’armement, or Directorate general of armaments) in association with the Franco-German research institute, Saint-Louis. Embedded electronic technology was adapted to create Bionear, a product aimed at the civil and industrial market. “This is a connected and made-to-measure intra auricular device aimed to help augment the capacity of the human ear.”
On the Asian market, Japan and South Korea are ground-breaking. They are strongly oriented towards innovation and experience very little turn-over in staff by encouraging loyalty.
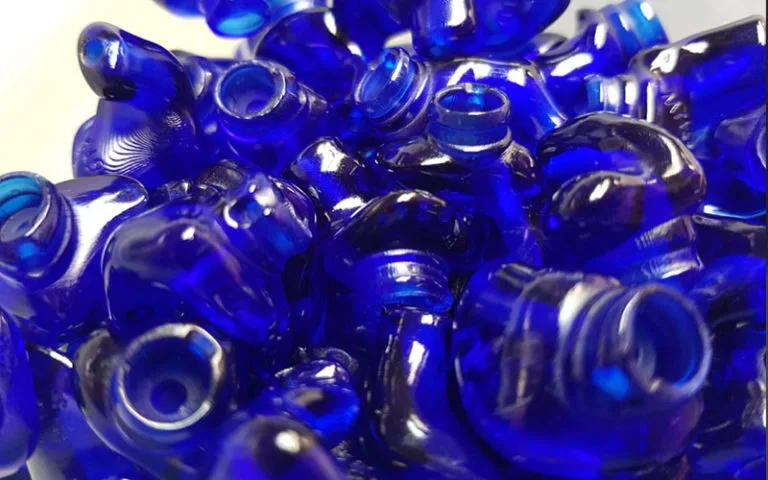
Cotrel Labs is also looking to contribute to the social, societal, and environmental goals and it encourages its clients to meet their Corporate Social Responsibility (CSR) challenges. For example, in 2021, an average member of staff used 400 pairs of throwaway earplugs. By offering a made-to-measure auditive protection, and guaranteed for 6 years, Contral Labs assists businesses in the development of their sustainable practices. As such, every year, 31 000 businesses choose the Norman company to guarantee the health and security of their staff with sustainable products, which are comfortable and easy to use.
Thematics