Published on 07 May 2024
Reading time: 4 min.
We got the good news at the end of 2022… Following in the footsteps of Eastman, the Belgian brand Futerro announced it was coming to the Port-Jérôme business park in Seine-Maritime. What’s the idea? To open the world’s first industrial facility producing, processing and recycling bioplastic. It brings the circular economy and energy transition together: let’s find out more about an exciting new project in Normandy!
History and expertise
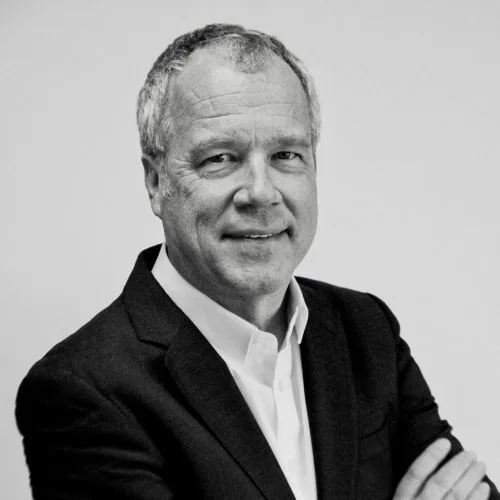
Galactic was founded 30 years ago in Brussels and was the first company to manufacture lactic acid (the same stuff as inside our bodies) by fermenting sugar. “We started out in a tiny lab before founding Galactic to sell it as a food preservative,” says Frédéric Van Gansberghe, CEO and co-founder of the company. Lactic acid is manufactured on an industrial scale in fermenters containing water, sugar and bacteria. “Bacteria is what turns the sugar into lactic acid.”
The company’s researchers used their expertise in lactic acid production to form Futerro. The affiliate was founded in 2007 to develop new products using lactic acid to make PLA or polylactic acid for the chemical industry and plastics production.
The bioplastic can replace a huge amount of petroleum-based plastics depending on function. “We have to reduce our carbon footprint now to cut global warming, so we have to find solutions to combat the impact of fossil fuels,” says the CEO. Since PLA is a plant-based or bio-based plastic that can be recycled indefinitely, it’s the first port of call. “It has the exact same properties as virgin polyester once recycled. It’s very similar to the likes of PET and polystyrene. It can easily be used in food packaging or the fibre industry. It’s actually better in some instances, i.e. 3D printing, than current petroleum-based plastics.”
After a pilot project in Belgium fine-tuned the process, Futerro opened its first factory in China. ”It’s the world’s biggest lactic acid factory to date with a 200,000 ton capacity and fuelled by corn. It supplies the Futerro factory so it can make biopolymers or bioplastics. It has a 100,000 ton capacity making it the second biggest facility in the world,” says Frédéric Van Gansberghe.
A one-of-a-kind factory
The Belgian company explored several locations (twenty sites in a dozen countries!) before choosing to open its European facility in Normandy, specifically the Caux Seine Agglo area and Port-Jérôme business park. Futerro has an estimated investment of 500,000,000 euros and 26 hectares where it plans to build three integrated factories to produce lactic acid, turn it into PLA and recycle end-of-life PLA ready to re-use. It has been helped on its way by AD Normandie, river freight on the Seine, nearby Le Havre port, an exciting ecosystem, industries in the process of decarbonisation and other assets that Normandy has going for it, alongside the extensive farmland it needs for production.
“We’re not going to starve people,” smiles Frédéric Van Gansberghe, reminding us that “80% of land is used to produce meat. But we do have to reduce how much meat we eat. The human body needs protein to function, so we have to find it elsewhere. Wheat is a good solution because it contains starch, which we use to make sugar to produce our bioplastics, as well as protein and fibre that stay in the food industry.”
A historic partnership
In mid-2024, the CEO of Futerro announced their past partnership with Tereos, the leading French sugar and starch group. 150,000 tons of dextrose (glucose derived from wheat starch) are expected to be directly produced starting from 2027 at one of the group’s sites in Lillebonne, to supply the biorefinery. The two partners will jointly finance the construction of a 1.5-kilometer pipeline, which will link the two plants. A truly unique circular economy partnership in Europe, serving decarbonized chemistry!
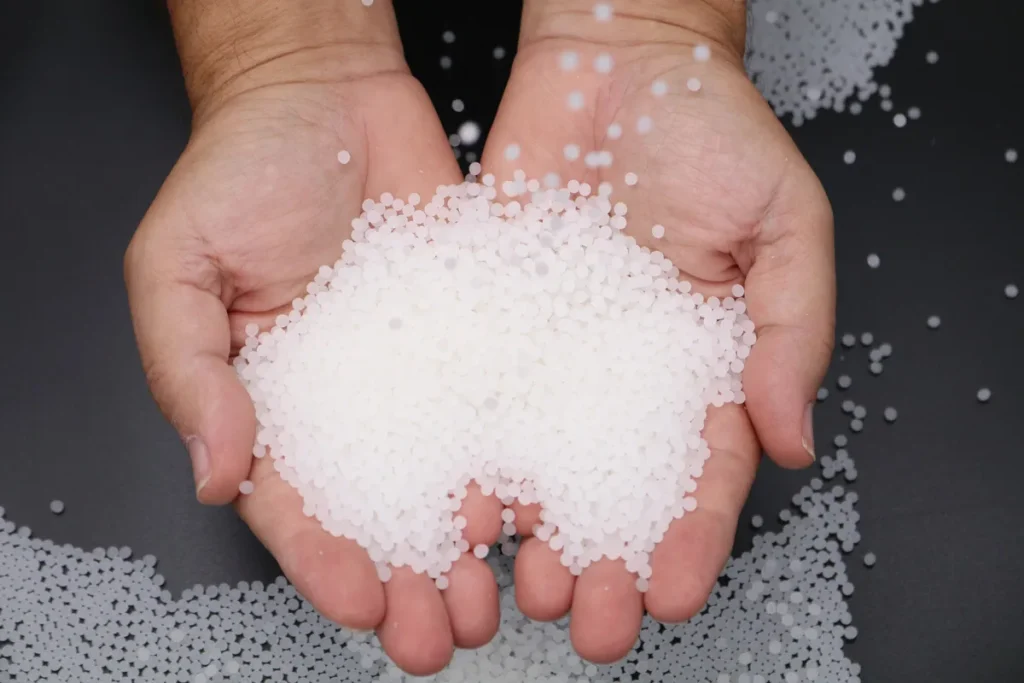
This one-of-a-kind project stands out from its Chinese counterpart as it has an on-site recycling facility. “PLA is a polymer with two interesting end-of-life properties: you can compost it industrially so it decomposes within three months or you can recycle it to make more lactic acid and virgin PLA.” The innovation to recycle all PLA in the long-term comes from the Belgian company and is called Loopla®.
Another thing that stands out is its impact on the planet. The Belgian company is true to its word and proud to have a low carbon footprint. “We produce 80% less carbon than petroleum-based polymers by using biogenic carbon (carbon that is stored in biological materials). Moreover, we want to produce our own energy in Port-Jérôme using wood or plant-based materials to cut gas and petrol out completely and reduce our products’ carbon footprint even more,” concludes the CEO.
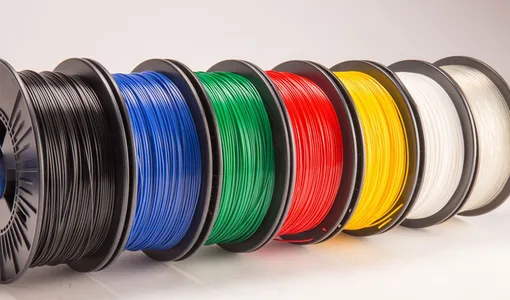
Good to know
Plastic is a material that we use a huge amount of: it’s the 3rd most used material in the world after cement and steel and is showing no signs of slowing down.
The world now produces approximately 500 million tons of plastic and estimates put it at 1 billion tons by 2050.
Initial consultations should begin soon as the company wants to get a building permit in 2024 to open its factory in early 2026.
The factory will produce 75,000 tons of PLA to begin with. In the long term, it will create 250 direct jobs.
Did you find this content useful?
Thank you
Thank you for taking the time to let us know that you found this content useful. Your encouragement is important to us, and your feedback helps us to improve.
Thank you
Thank you for taking the time to let us know that this content was not useful to you. We apologise for any inconvenience.
Share this content
Share this content
You might also like
- Caen
- Calvados
- Energie
- Innovation
- International
GANIL, a leading research facility for nuclear physics
Published on 26 May 2025
Reading time: 5 min.
- Cherbourg
- Green Normandy
- International
- Manche
- Maritime & freight industry
Jérémie Morizet and Clément Schapman set a deep-sea exploration record
Published on 06 Jan 2025
Reading time: 9 min.
- Green Normandy
- Industry
- Innovation
- International
- News
Normandy’s manufacturing industry is committed to the future
Published on 10 Dec 2024
Reading time: 2 min.
- Energie
- Fécamp
- Innovation
- Seine-Maritime
- Study
Campus Normandie Eolien: a unique training venue
Published on 10 Dec 2024
Reading time: 5 min.
- Aeronautics & Space industry
- Defense & security
- Green Normandy
- Innovation
- Le Havre
Safran Nacelles clears decarbonisation for take-off near Le Havre
Published on 03 Dec 2024
Reading time: 4 min.
- Fécamp
- Food industry
- Food processing
- Gastronomy
- International
Published on 29 Nov 2024
Reading time: 5 min.
- Fécamp
- Food processing
- Gastronomy
- Heritage
- Seine-Maritime
Palais Bénédictine, entrepreneurial spirit
Published on 29 Nov 2024
Reading time: 4 min.
- Caen
- Calvados
- Doing business
- Green Normandy
How the general public supports bioplastics research in Normandy
Published on 20 Nov 2024
Reading time: 4 min.